Àdìrę is Yoruba which translates to “tie and dye” in English is a type of dyed fabric made by various dye resist methods and is mostly popular in the South-western part of Nigeria. In Yorùbá land, Àdìrę plays a dual role as a fashion statement and a visual language. It is means of artistry and telling stories because it dates back to the 18th century and it holds years of cultural artistry. A professional decorator of Adire is traditionally referred to as “Alidire” and the craft is passed down from generation to generation.
Folklore about Àdìre
In Yorùbá traditional history, it is said that Orunmila, the Yorùbá deity of wisdom and divination was divinely inspired to create patterned dyed cloths using the design of certain birds, namely Agbe, Àlùkò, Odídęrę, Lekeleke and Agbufon. He was also permitted to use indigo, cam wood, palm oil, chalk and variegated colour pigments in the creation. These colours affects the production of the adire because till date although adire can be found in almost any colour the most popular colors are the bluish-purple, red, orange, and green which are the original colors.
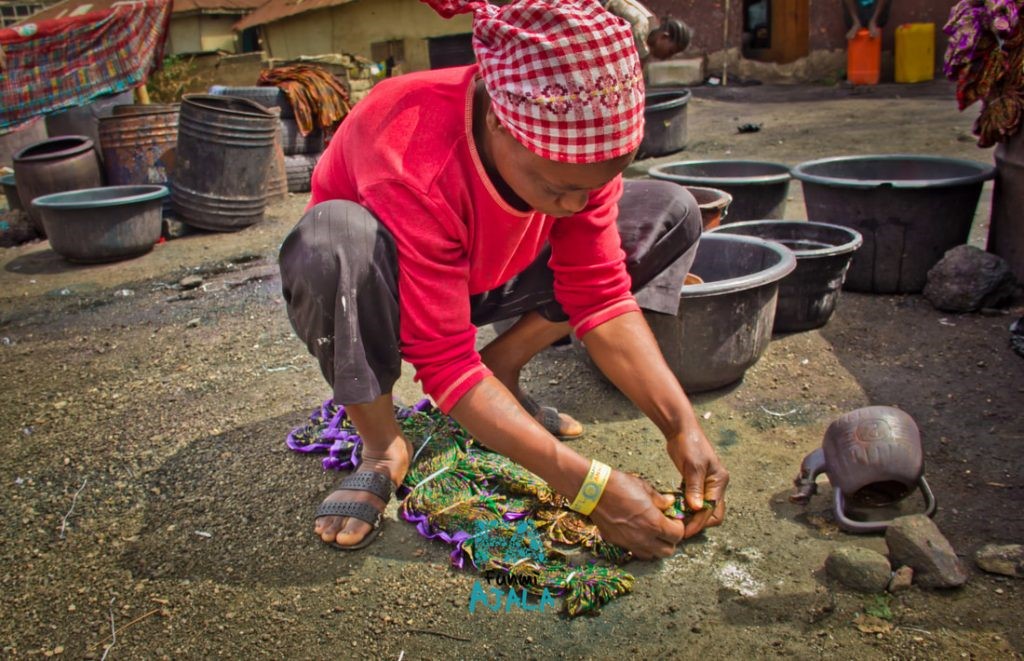
Although according to scholarly opinions, the origin of Àdìrę is said to be unknown, however, there exists a battle between the people of Abeokuta and Osun State about who first invented the adire. Women were mostly the Àdìrę artists although they were a few men. Àdìrę was first made from a hand-woven cloth called Kíjìpá. This cloth was then dyed with indigo colour or aró. Women were at the forefront of weaving the fabric and indigo-dying them using the Oniko method. Apart from the freshly made Adire fabrics, old clothes were refurbished and dyed for the people who could not afford the new ones and were sold at a cheaper rate.
Between 1880 and 1925, Àdìrę artists started using calico for their products due to the importation of English cotton products. The then British government in Nigeria heavily taxed the local Kíjìpá fabric and left the imported fabrics untaxed. This interestingly led to the expansion of the Àdìrę industry as a new method of production became innovated, the “starch resist” method called ‘Eleko’in Yoruba language.
By the 1930’s, another innovation was birthed with the Àdìrę art being done on fabrics such as Brocade and Velvet. The introduction of sewing machines in the 1930s also birthed the entry of men into the otherwise female-dominated Àdìrę industry.
Sadly, The 1940s and 1950s brought a decline in production of adire due to factors such as the ban on the importation of textiles due to World War II, the universal free education policy which meant that all children had to go to school and apprenticeship was affected, a rapid population growth which led to the conversion of Àdìrę courtyards for other purposes and the flooding of the Nigerian market with Àdìrę imitations.
After World War II, new brightly coloured chemical dyes were introduced and this marked a resurgence and a new beginning for the Adire tradition. It became very popular in the 1960s and also became a national identity for Lagos elites who were protesting against European values.
Over the years, Àdìrę has remained fashionable, and the methods of production have evolved as seen from the textile choices and technology behind the methods.
After folding the clothes, they will put it in starch. We use fabrics like Daviva, Evaporated, and cotton materials in short.
They will first of all design the material by tying it up before soaking it in starch. Starch makes the dye penetrate and stay in the clothes. Some materials are first starched before designing, while some are soaked in water before soaked in dye, this allows for better penetration of the dye.
After being soaked in dye it is now spread out to dry off. After drying, one needs to properly shake off the stones and dirt on the materials that are glued on as a result of the starch and where the cloth is spread.
Àdìre Techniques and Methods
A special kind of dye is used called ‘Elu- Aja’ botanicaly called Lonchocarpus Cynescens it is commonly found in North-Western Nigeria. These leaves were pounded, shaped into balls, and sundried before sale. It is then mixed with local chemicals and allowed to ferment within four weeks to six months depending on the nature of the dye after which the dye produces a blue-purple color, Indigo.
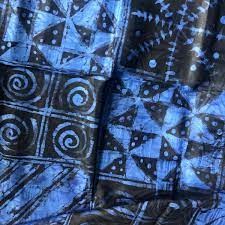
Through the years, different dye resist methods have been introduced but Àdìrę Oniko and Àdìrę Eleko are the oldest forms.
Adire Oniko makes use of raffia which is strategically tied at different positions of the fabric to create a pattern, the raffia could be tied individually around the cloth or tied around objects. Objects such as pebbles or dried seeds of some fruits. The Oniko method has evolved over the years to several subgroups which have come about as a result of experimentation using the original Oniko method. These subgroups are circles, Eleso, Sabada, Clamping, and Stitching. This method refers to the process of tying a pattern onto the cloth prior to dyeing with raffia or thread. This effect can be achieved by pressing the finger through the cloth, and then tightly tying this area with cotton or raffia to prevent any dye from entering the area. The raffia provides a means of dye resistance when the fabric is finally dyed.
The Eleko method makes use of cassava paste or starch paste which provides the dye resist means. The cloth is hand painted using the paste and a wet feather or brush. Different types of motifs were usually hand painted on the fabrics, the motifs were usually stylized representations of plants, animals, lines, shapes, and celestial bodies as well as everyday objects drawn by hand or stencils made from leaves. After the process, it was sun-dried for two days before being immersed in the dye solution, and it will take roughly three to five days to complete the yard. All these representations reflected the Yorùbá way of life. The Eleko method has also been developed into different subgroups: Freehand Eleko, Stenciled Àdìrę Eleko, Eleko Splash, and Lace Eleko.
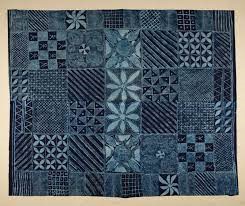
More modern methods of Àdìrę are: Batik, Factory produced Àdìrę and discharge dyed Àdìrę. The Batik method uses wax as a means of dye resistance and takes less time. Its subgroups are Freehand Batik, Splash Batik Àdìrę Olonte, and Batik as an art form.
The factory-printed Àdìrę are replicated Adire motifs printed in the factory.
Oftentimes, there is a slight discord as to Kampala and Adire. They are the same, the name “Kampala” as Àdìrę is often called came to be because of the Peace Conference held in Kampala, Uganda to settle the Biafra war in Nigeria. Àdìrę became popular in Nigeria during that period.
A group of women that specialized in Àdìrę Eleko in Ibadan, Nigeria produced a popular design used for Àdìrę known as Ìbàdàndùn which means Ibadan is sweet. So here it is, a brief walk through one of the ancient art of Adire, an embodiment of culture and fashion not just in Nigeria but in Africa.
We appreciate your contribution.
Join the Oriire Community
Become a free member to get the monthly roundup, unlock more challenges, comment on articles and bookmark your favourites
Share
0 Comments